- A+
試驗研究了聚四氟乙烯密封圈壓縮量、檢漏時間等因素對密封性能的影響;利用數值模擬方法研究了氦氣在聚四氟乙烯密封圈中的滲透過程及密封圈尺寸對該過程的影響;分析探討了含氦滲透率較高材料容器的檢漏問題。研究結果表明,試驗中容器檢漏測得的漏率主要是聚四氟乙烯密封圈對氦氣的滲透產生的,充氦到檢漏之間的時間過長使得氦滲透漏率較大,導致容器的漏率不能滿足設計指標;縮短充氦到讀取檢漏值的時間,在氦氣還未滲透通過密封圈前就檢漏可獲得界面、漏孔泄漏導致的漏率,增大密封圈滲透方向的厚度可顯著增加該時間。
聚四氟乙烯(PTFE) 材料具有優良的耐蝕性、耐候性、化學穩定性,并且不沾、無毒、無污染,被稱為“塑料之王”,是一種較好的密封材料,廣泛應用于國防、航空航天、醫學、石油化工、電子、機械等許多領域的密封裝置上。同時,PTFE 材料還具有優良的耐輻照性、氚相容性以及對氚的低滲透率性,因此也廣泛應用于含氚系統的密封。
在某含氚部件的包裝容器中采用了PTFE 材料作為密封圈,在生產過程中發現發現包裝容器的整體氦漏率不滿足要求。為分析該問題產生的原因,開展了密封圈密封性能試驗,研究了PTFE 密封圈壓縮量、檢漏時間等因素對密封性能的影響,并利用數值模擬方法研究了氦氣在PTFE 密封圈中的滲透過程及密封圈尺寸對該過程的影響,探討了含氦滲透率較大的密封材料的氦檢漏問題。
1、試驗過程
1.1、試驗容器
設計了如圖1 所示的模擬容器用于測試密封圈的密封性能。模擬容器的法蘭密封結構及容積與產品包裝容器完全相同,為了盡量減少其它因素的干擾,模擬容器上蓋為非焊接全金屬結構,容器與外部的氣路連接采用金屬墊密封,閥門為全金屬兩通手動閥。氦檢漏檢測表明,該模擬容器的標準漏率( 不含密封圈) 小于1 ×10-10?Pa·m3/s,排除了容器本身的泄漏問題。
1.2、PTFE 密封圈
PTFE 密封圈由三種外購的PTFE 棒料加工而成,以A、B、C 表示,其尺寸均為外徑Φ178 mm、內徑Φ170mm、厚度3 mm。
1.3、檢漏
通過測量模擬容器上下法蘭的間隙變化來確定PTFE 密封圈的壓縮量,模擬容器裝配好后,其內部抽真空后充入0.05 MPa 的氦氣,然后將模擬容器裝入檢漏容器中,采用壓力真空室法對模擬容器進行整體漏率檢測,具體測試方法、步驟和條件均依據國軍標GJB/Z 221 -2005《軍用密封元器件檢漏方法實施指南》。檢漏儀為美國瓦里安PR02 型氦質譜檢漏儀,檢漏時采用瑞士安維CL004?標準漏孔進行標定。
2、試驗結果及分析
2.1、試驗結果
2.1.1、密封圈的漏率及壓縮量對漏率的影響
對三種密封圈進行了不同壓縮量下的漏率測試,壓縮量從0.6 mm 到1.15 mm,其充氦4 h 以上的穩定氦漏率值如表1 所示。其中,對材料C 密封圈0. 7 mm壓縮量下的漏率值進行了重復性測試,4次的漏率值為3.1 ×10?-7, 3.2 ×10?-7, 3.3 ×10?-7, 3.6 ×10?-7?Pa·m3/s,重復性相對較好,因此其它檢測未做重復性測試。測試結果表明,三種PTFE 密封圈的密封性能存在一定差異( 范圍在1.4 × 10-7?~ 6.1 × 10?-7?Pa·m3/s) ,但還是比較接近的,均在10?-7?Pa·m3?/s 量級;同時,提高壓縮量可提高密封性能,但提高的幅度較小。
2.1.2、檢漏時間對密封圈漏率的影響
利用密封圈A 研究了檢漏時間對檢漏值的影響,試驗容器按照密封圈壓縮量0.6 mm 裝配,容器內充氦后立即置于檢漏容器中進行檢漏,記錄檢漏值,檢漏值隨檢漏時間的變化曲線如圖2 所示。可以看出,初始時容器的最低漏率可達到1.5 ×10-9?Pa·m3/s,隨著檢漏時間的延長,漏率值迅速上升,約30 min 后漏率值上升趨勢緩慢,60 min 時漏率值達到2.7 ×10?-7Pa·m3?/s,在經過17 h 后,漏率值穩定在4.8 ×10?-7?Pa·m3?/s,圖中在1 ×10?-7?Pa·m3/s 漏率值處出現的拐點是檢漏儀檢漏模式切換導致的。
更換同一種密封圈,試驗容器按照密封圈壓縮量0.8 mm 裝配,充氦后臨時放置了約30 min 然后再開始檢漏,檢漏值隨檢漏時間的變化曲線如圖2 所示。可以看出,兩種壓縮量下密封圈漏率值的變化規律相近,但壓縮量為0.8 mm 時初始的漏率顯著增大( 達到4.3×10?-8?Pa·m3/s) ,這可能是由于充氦后沒有立即檢漏,放置了約30 min 導致的。
2.2、試驗結果分析
根據以上試驗結果,PTFE 密封圈的漏率值是隨著檢漏時間的延長而增加的,只有經過較長的時間后才會達到一個穩定值,不同PTFE 密封圈的穩定漏率值有一定差異,適量增加密封圈的壓縮量可小幅度提高其密封性能。
根據以上結果,可初步判斷模擬容器檢漏測得的漏率主要是由氦氣透過PTFE 密封圈而產生的。
3、PTFE 密封圈密封性能的計算分析
3.1、PTFE 密封圈穩態氦漏率計算分析
以上初步分析表明,模擬容器檢漏測得的漏率主要是由氦氣透過PTFE 密封圈而產生的。徐懋等[6]的研究表明,氫氣、氦氣等氣體在PTFE 材料中的透氣過程本質上是氣體在材料中的滲透擴散過程。在滲透擴散機制下,PTFE 平墊密封圈的穩態氦滲透漏率QP可通過以下公式計算得出
式中,CP為PTFE 材料中氦氣的滲透系數,m2/s;Δp 為密封圈兩側的氦氣分壓差,Pa;AP為密封圈墊中氦氣滲透方向的面積,m2?;δ 為密封圈中氦氣滲透方向的厚度,m。
對于本文研究的PTFE 密封圈,當壓縮量從0.6 增加到1.15 mm 時,密封圈墊中氦氣滲透方向的面積減少了23%,密封圈中氦氣滲透方向的厚度增加了30%,由式(1) 可知,相應的滲透漏率將降低41%,這與試驗結果較為吻合,說明通過增加密封圈的壓縮量來降低漏率,幅度是比較有限的。
3.2、PTFE 密封圈氦漏率隨時間變化分析
采用描述氣體在固體中滲透擴散規律的菲克第二擴散定律,可對檢漏氣體氦通過PTFE 密封圈的滲透量隨時間變化行為進行計算。根據密封圈的尺寸( 考慮到密封圈被壓縮0.6 mm、其寬度由4 變為5 mm) 、氦氣在PTFE 材料中的滲透系數( 按8.5 ×10?-11m2/s 考慮)以及密封圈兩端的氦氣分壓,采用Fluent 軟件計算得到容器的氦漏率隨時間的變化曲線,如圖3(a) 所示。從計算曲線看,在充氦的十多分鐘內,氦氣尚未滲透到達密封圈的外側,因此漏率非常小(小于1 ×10?-10?Pa·m3/s) ,隨后快速上升,在約15 min 時達到1 × 10?-9?Pa·m3/s, 30 min 后上升速率明顯減緩, 40 min 時漏率約為1 ×10?-7?Pa·m3/s。
對于實際檢漏來說,充氦后要將被檢容器裝入檢漏容器中,連接上檢漏儀,然后對檢漏容器抽真空,抽真空到一定水平后檢漏儀才能檢得較小的漏率值,這些操作需要一定的時間。為此將圖3(a) 中的時間扣除約15 min,再與試驗結果(圖2 中壓縮量為0.6 mm 的曲線) 進行對比(如圖3(b) ) ,可以看出,兩者的數據比較吻合。這個計算模擬結果表明模擬容器的漏率值隨著檢漏時間的延長而增加、在經過較長的時間后達到穩定值這一現象是滲透擴散特性決定的。
3.3、PTFE 密封圈厚度與氦漏率變化關系分析
根據菲克擴散第二定律,滲透擴散方向的厚度對滲透擴散的動態過程有十分重大的影響。為此采用數值模擬方法研究了密封圈厚度對檢漏時間及漏率的影響,仍采用上述密封圈的基本結構尺寸,但密封圈寬度( 即滲透方向的厚度) 分別為2.5,5,7. 5和10 mm,四種結構密封圈滲透漏率隨時間的變化曲線如圖4 所示。可以看出,密封圈滲透方向的厚度從2.5,5 增加到7.5,10 mm 時,氦滲透到檢漏儀可檢漏率( 考慮到抽真空時間、真空度等因素,按1 × 10?-9?Pa·m3/s 考慮) 的時間從4 min 顯著增加到16,38,71 min。上述數值模擬結果可以從擴散第二定律得到解釋。密封圈內部氦氣向外擴散過程可近似簡化為半無限長棒擴散模型,其邊界條件為:x = 0,c = c0;x = ∞,c=0,擴散方程的解為
式中, erf( ) 為誤差函數;c 為某一時刻、某一位置密封圈內的氦氣含量;c0為密封圈高壓端的氦氣含量;D 為擴散系數,即為PTFE 中氦氣的擴散系數,m2?/s;t 為擴散時間,s。
根據上述方程解,擴散達到同一濃度時,不同條件的x /(2Dt) 應相等,即擴散層深度與擴散時間的平方成正比,因此當擴散深度增加1 倍時,擴散達到同一濃度所需的時間將增加到原來的4 倍,上述數值模擬結果與此結論比較吻合。上述計算模擬和分析結果表明,增大密封圈滲透方向的厚度可顯著增大氦滲透的時間。
此外,根據式(2) ,滲透擴散達到同一濃度時,滲透擴散所需的時間與擴散系數成反比,如果氦在密封圈材料中的擴散系數D 很小,則氦滲透到檢漏儀可檢漏率的時間很長,上述試驗中出現的問題在一般的檢漏過程中很難發生。
4、含氦滲透率較高材料的容器的檢漏問題探討
根據以上試驗結果及計算模擬結果,采用PTFE材料作為密封圈的密封容器,由于氦氣對PTFE 材料的滲透系數較大,約為其它非金屬密封材料的幾十倍以上,其氦漏率隨著檢漏時間的延長而顯著增大。一方面無法讀取較穩定的檢漏值,另一方面氦漏率值較大,無法滿足設計要求。這種問題在其它含有對氦擴散系數較大的非金屬密封材料容器的檢漏中也存在,如何對這類容器進行密封性能檢漏是普遍存在的問題。
一般檢漏的目的是檢測密封容器的加工質量、裝配質量是否滿足要求,即應檢測因這些問題而導致的界面、漏孔泄漏問題。如果將穩定氦漏率作為檢測值,在容器其它密封環節沒有問題的情況下實際檢測的漏率為氦氣在非金屬密封材料中的滲透速率,并且在大多數情況下,氦滲透產生的漏率明顯大于氦泄漏產生的漏率,這樣導致泄漏因素被滲透所掩蓋,無法達到檢漏目的。本研究中容器的漏率不滿足要求的原因就是充氦到檢漏之間的時間過長導致氦滲透量較大掩蓋了容器自身的泄漏情況。為此應在檢漏儀的反應時間足夠的情況下盡量縮短充氦到讀取檢漏值的時間,在氦氣還未滲透通過密封圈前就獲得檢漏值,測得的結果基本上可以反映界面、漏孔泄漏。
但氦氣還未滲透通過密封圈的時間與密封圈滲透方向的厚度有十分密切的關系,根據3. 3 節的模擬和分析結果,如果密封圈滲透方向的厚度過小,氦氣滲透的影響在很短的時間內就產生了( 如3.3 節中密封圈厚度為2.5 mm 的結果) ,根本來不及測出界面的泄漏,檢測結果不能反應真實的泄漏。如果設計時將密封圈的寬度( 即滲透方向的厚度) 增加,密封圈內氦滲透到檢漏儀可檢漏率的時間將顯著增加,將有比較充足的時間進行檢漏,從而可獲得較為準確的泄漏漏率。
5、結論
(1) 試驗中容器檢漏測得的漏率主要是PTFE 密封圈對氦氣的滲透擴散產生的,不同PTFE 密封圈的滲透漏率有一定差異,但均在10-7?Pa·m3/s 量級;增加PTFE 密封圈的壓縮量可小幅度減小其氦漏率值。
(2) 試驗中容器的漏率值隨著檢漏時間的延長而增加,在經過較長的時間后達到穩定值,這一現象是由氦氣在密封圈材料內的滲透擴散特性決定的。
(3) 由于氦在PTFE 材料中的滲透系數比較大,導致氦滲透通過密封圈的時間較短,密封圈中的氦滲透很容易干擾密封面泄漏的檢測。若要獲得泄漏導致的漏率,應盡量縮短充氦到讀取檢漏值的時間,在氦氣還未滲透通過密封圈前就獲得檢漏值。本研究中容器的漏率不滿足要求的原因就是充氦到檢漏之間的時間過長導致氦滲透量較大掩蓋了容器自身的泄漏情況。
(4) 密封圈滲透方向的厚度對氦滲透到檢漏儀可檢漏率的時間有顯著影響,過小的厚度將導致無法測出界面的泄漏;增大厚度,可有比較充足的時間進行檢漏,從而可獲得較為準確的界面、漏孔泄漏漏率;
(5) 上述現象在其它含有對氦滲透系數較大的非金屬密封材料( 如氟橡膠密封圈等) 容器的檢漏中也發現過,上述結論同樣適用。
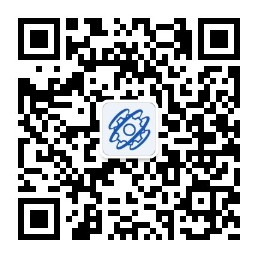